The Comprehensive Guide to Vacuum Presses and Their Essential Components
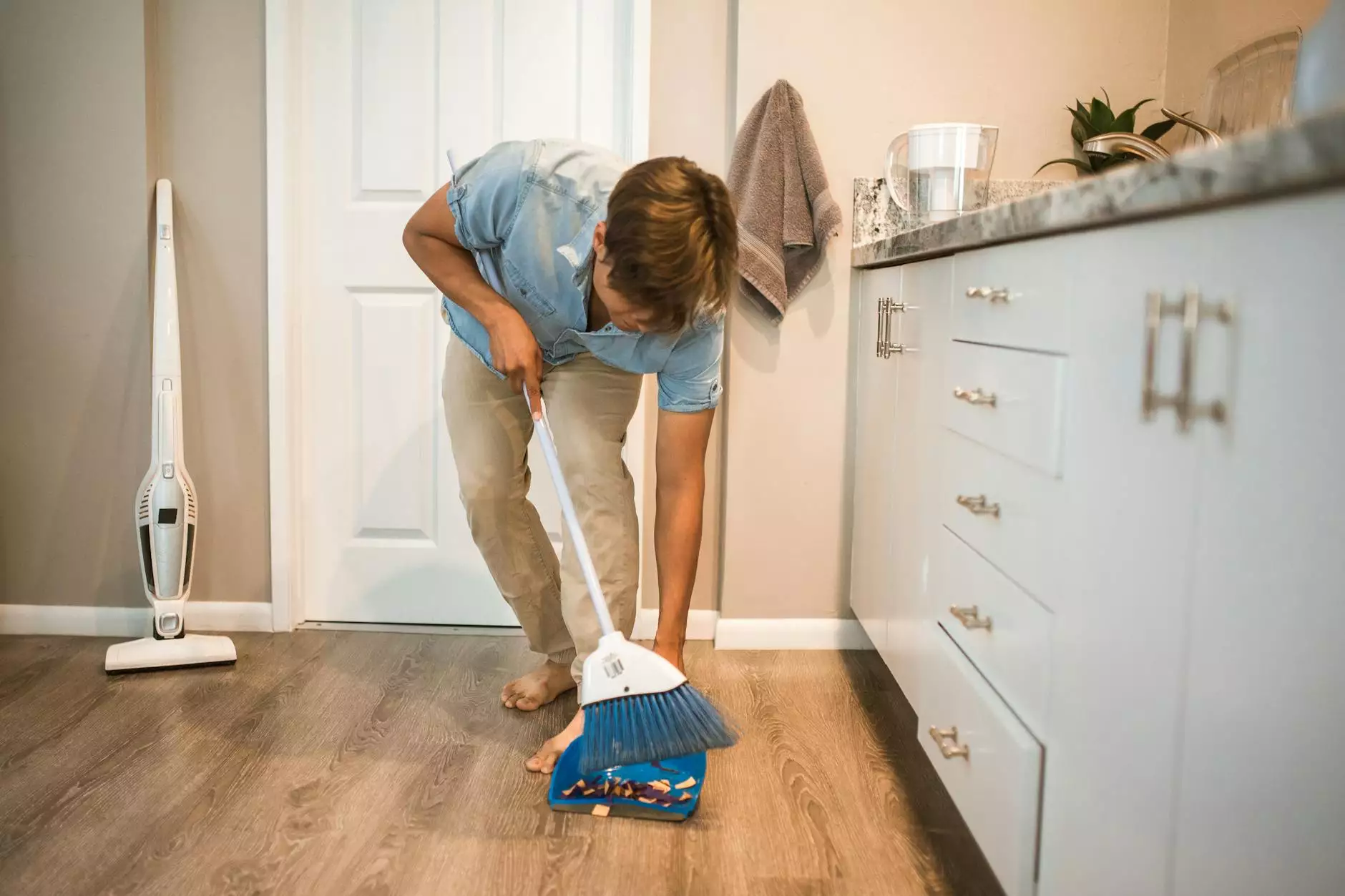
In the realm of manufacturing and prototyping, vacuum presses play a pivotal role. They enhance productivity, ensure precision, and foster innovation in a multitude of industries. As businesses seek to streamline their operations and improve product quality, understanding the intricacies of vacuum systems and their components becomes essential. This article delves into the various aspects of vacuum presses, emphasizing the importance of components such as membranes, silicone membranes, rubber membranes, and vacuum system parts. Notably, we will explore the significance of the numbers 15000 and 2000 in this context.
Understanding Vacuum Presses
A vacuum press is a machine that uses atmospheric pressure to create a bond between materials. By removing air from a chamber, the press can apply significant pressure on the materials being worked upon. This is particularly valuable in industries such as woodworking, automotive, and composites, where strong, uniform bonds are necessary.
The Mechanics Behind Vacuum Pressing
The functionality of a vacuum press is often guided by three core components: the vacuum pump, the pressing chamber, and the membrane. Each of these parts plays an integral role in ensuring optimal performance.
The Role of the Vacuum Pump
The vacuum pump is tasked with removing air from the pressing chamber. There are various types of vacuum pumps, including rotary vane pumps, diaphragm pumps, and liquid ring pumps. Each type offers unique advantages depending on the application, from low maintenance to higher efficiency.
The Pressing Chamber and Its Design
The design of the pressing chamber significantly influences the effectiveness of the vacuum press. Factors such as size, material, and internal geometry must be considered to facilitate even pressure distribution and maximum efficiency.
Importance of Membranes in Vacuum Presses
Membranes serve as the interface between the material being compressed and the vacuum environment. They ensure that even pressure is applied across the surfaces of the material, which is critical for achieving a strong bond. The selection of the right membrane can greatly affect the quality of the finished product.
Types of Membranes Used in Vacuum Presses
When it comes to buying membranes, understanding the different types available is crucial. Below, we explore the diverse kinds of membranes suitable for vacuum presses.
1. Silicone Membranes
Silicone membranes are highly versatile and are prized for their durability and resistance to heat and chemicals. Their flexibility allows them to form a tight seal, making them ideal for applications that require precise pressure application. Additionally, silicone membranes are easy to clean, which is essential for maintaining hygiene in many industries.
2. Rubber Membranes
Rubber membranes offer excellent elasticity and strength. They are effective in creating a solid vacuum seal, particularly in woodworking and automotive applications. Their resilience helps in coping with varying temperatures and pressures. When selecting rubber membranes, businesses should consider factors such as thickness, durometer, and material composition to ensure compatibility with their specific application.
3. Natural Rubber Membranes
Natural rubber membranes are favored for their environmental friendliness and biodegradability. They are suitable for applications requiring flexibility and strength. Although they may not have the same temperature resistance as synthetic membranes, they provide a cost-effective option for certain applications, particularly in eco-conscious operations.
Vacuum System Parts and Their Significance
A vacuum press consists of various crucial parts that contribute to its overall functionality. When optimizing your vacuum system, paying attention to these components is vital.
Essential Vacuum System Parts
- Vacuum Gauge: This instrument monitors the pressure inside the vacuum chamber, ensuring that optimal conditions are maintained.
- Seals and Gaskets: These components help in preventing air leaks in the system, which can sabotage vacuum integrity.
- Control Panel: The control panel allows operators to manage and adjust settings, providing flexibility in the vacuum process.
- Valves: Valves control the flow of air and materials in and out of the vacuum system, making them essential for operational efficiency.
- Filters: Filters are crucial in preventing contaminants from entering the vacuum system, which could lead to equipment damage or product quality issues.
Why Choose the Right Components for Your Vacuum Press?
Choosing the correct components, from membranes to vacuum system parts, directly impacts the performance and outcomes of vacuum pressing. Investing in high-quality materials may have a higher upfront cost, but will ultimately lead to enhanced efficiency, reduced downtime, and superior product quality.
Cost Considerations: The 15000 to 2000 Ratio
When contemplating upgrades or new purchases, businesses often weigh their options against budget constraints. The numbers 15000 and 2000 can serve as performance benchmarks in evaluating costs vs. benefits.
For instance, suppose a vacuum press with an annual operational cost of $15,000 performs optimally amidst various production challenges. In contrast, a cheaper alternative at $2,000 might compromise efficiency, longevity, or output quality, prompting operations to rethink their investment strategy. Therefore, a higher initial cost can often yield better long-term savings through durability and efficiency.
Future Trends in Vacuum Press Technology
The landscape of vacuum pressing technology is continually evolving, with innovations that enhance efficiency, reduce costs, and incorporate sustainability. Businesses must stay abreast of trends to remain competitive and leverage new technologies as they arise.
Innovations in Membrane Materials
Research is ongoing into advanced materials for membranes that offer even greater durability and performance. Companies are investing in R&D to produce membranes that can withstand more extreme conditions while maintaining a sustainable profile.
The Role of Automation
Automation plays a pivotal role in optimizing the performance of vacuum presses. Automated systems can monitor and adjust settings in real-time, leading to improved consistency and efficiency in production runs.
Conclusion
In conclusion, understanding the intricacies of vacuum presses, membranes, and system components is essential for any business looking to maximize its operational efficiency and product quality. By investing wisely in these technologies, and keeping in mind the significance of numbers like 15000 and 2000 in your cost-performance analysis, you can ensure that your business remains at the forefront of innovation and productivity.
Call to Action
Visit vacuum-presses.com today to explore a wide range of membranes, silicone membranes, rubber membranes, and essential vacuum system parts that can elevate your production processes. Don't leave quality to chance—invest in the best!
15000 2000